I’m working on a new woodworking project that involved cutting through-slots for bolts in a couple of boards. The two boards will act as adjustable arms to hold a dowel handle for a garden cart.
- How To Create A Slot In Wood Floors
- How To Create A Slot In Wooden
- How To Make A Keyhole Slot In Wood
I have cut shorter and narrower slots using a table-mounted router for a coin bank. These bolt slots were considerably longer and 1/4' wide so I was reluctant to use the same technique. I don’t have a plunge router – which would probably be the fastest and easiest way to do this.
When the job calls for insertion of steel plates into timber, no other tool comes even close to cutting straight, parallel slots into wood. We also carry slotter chains and chainsets, including custom parts. Keyhole slots are a great way to hang a picture or plaque on a wall and are cut using a router and a keyhole bit. Learn how to set up your router and cut a keyhole slot.

Crowd-sourcing ideas
After checking a couple of woodworking forums for ideas – including one where someone trying this on a router table said the board 'shattered' (yikes!) – the general consensus seemed to be todrill out most of the material and clean up the slot later with a coping saw.
That sounded good (and safe) to me.
Since my slot was only 1/4' wide, I decided best approach was to use a 1/4' Forstner bit in a drill press to define the slot and remove most of the material, then clean up the slot with a file and sandpaper.
- This is because a router cuts wood with an unguarded, spinning, high speed blade. Secure the Wood. Ensure that the fence edge is straight and smooth. Any nicks or bumps along the fence edge will affect your channel. When using a fence to cut wood, you will often need to additionally support the wood as it is machined.
- Mark, cut and fine-tune curves in wood, using routers, saws and other simple tools, by following these expert techniques. You can master them quickly and easily and deliver first-class results. Screw the trammel to the center of your workpiece and cut out the circle with your router.
- The 'bandsaw box' approach: cut a thin slice off the bottom of the piece, then make a cut in from the side and around the opening you want to create. The small cut in the side can be glued closed, and the solid bottom can be glued back on, almost indetectably.
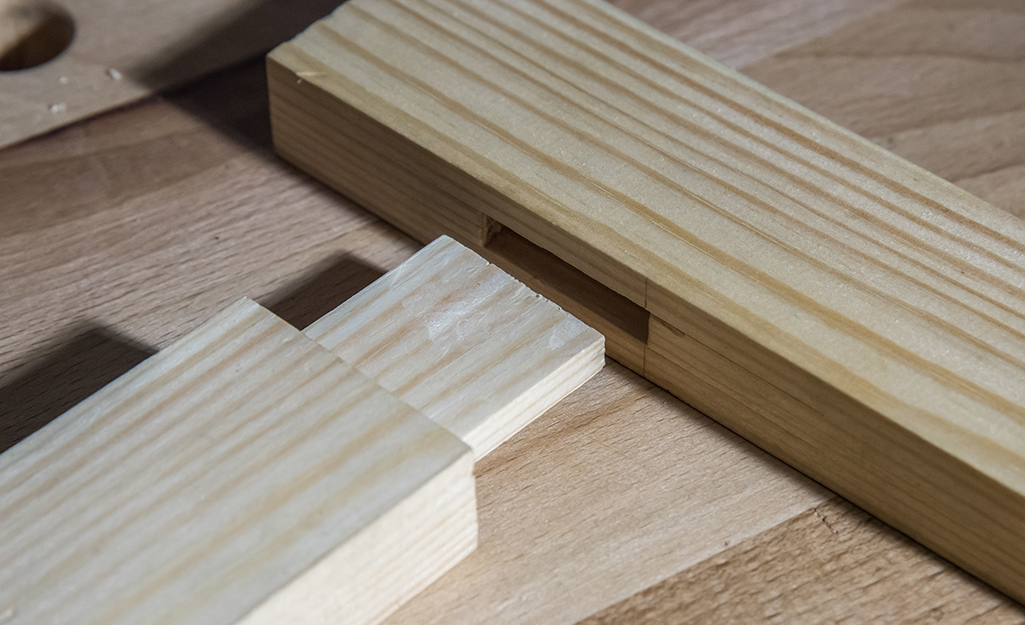
The shaft on the 1/4' bit was larger than the bit itself so I had to flip the board over to drill all the way through the 3/4' material. It’s probably a good idea to do this anyway to avoid tear-out unless you have a backer board underneath when you’re drilling.
What to do
Drilling
- Mark the centre points for each end of the slot in the blank and use a nail or awl to punch a small hole for orienting the bit.
- Set up the drill press with a Forstner bit the same size as the slot you’re cutting. You’ll need to attach a fence to the drill press table to maintain a straight line as you drill along the length.
- Place the blank against the fence and lower the bit. Adjust the fence and blank so the point of the Forstner bit enters the small punched hole. Clamp the fence in place, slide the blank to the mark at the other end of the slot and check that it’s aligned properly.
- Put a mark on the edge of the board that’s against the fence. Keep this edge against the fence when you flip the board over and drill the other side. This ensures the holes are in line even if your a hair off centre of the board.
- Turn on the drill press and drill the each end hole to define the slot – drilling about two-thirds to three-quarters of the way through the board. After that, just keep drilling holes and moving the work piece along the fence, overlapping holes just enough to keep point of the bit entering new wood. The slot will fill up with shavings which you should clear out if they get in the way.
- Once you’ve drilled the length of the slot, clean it out with a screw driver or something similar. Flip the board over (keeping the same edge against the fence).
- Repeat the process starting with the end holes. It doesn’t matter which direction you work in.
A COUPLE OF NOTES:
- If you’re making a wider slot, you may want to make an additional pass to remove the 'peaks' between holes.
- If you have a mortising chisel & bit you could swap that in once you’ve drilled the end holes.
Cleaning up the slot
- After the drilling is complete, clean out the shavings with an awl or small screwdriver.
- Clamp the work piece on edge to your bench and use a flat file to remove the high points left between the drilled holes being careful not to hit the rounded ends of the slots.
- Wrap a small piece of sandpaper around a drill bit (smaller than the slot) to sand the ends of the slot.
- After filing off most of the rough surfaces in the slot, wrap some sandpaper around the file and use it to finish cleaning up the slot.
If the slots were 1/2” wide or more, I probably would have used a jigsaw and straightedge to clean up the slots before sanding.
I originally had money in my bid to buy the Hema Chain Mortiser/Slot Cutter or Mafell Chain Mortiser/Slot Cutter for this timber framed, steel plate framed, barn in Portola Valley California. However, I had to lower may bid to get the job and I still needed a way of cutting the hidden 52 -- 3/8' x 8' deep steel knife plate slots in the timbers. I designed a slotter/mortise jig that I called the California Knife Plate Slotter - Mortiser for the 6x6 post and another jig that I called the Okie Knife Plate Slotter - Mortiser for the 5 1/2' x 9' GluLam Beams.
This is the first time I've assembled a roof structure without using any nails. Not even a nail to tack the exposed post or beams together. I had more problems with the bolt hole layout than making the knife plate slots.
Steel Knife Plates
Kerf Plates
Flitch Plates
Steel Plate Framing
California Knife Plate Slotter - Mortiser for the 6x6 post.
We slotted all of the 18-- 6x6 post in about 20 minutes with the California Knife Plate Slotter - Mortiser. However, we spent a lot more time on the countersink holes and thru bolt holes.
The chainsaw bar is attached to the jig with 3 -- 2 1/2' SDS screws thru the 1 3/4' x 2 9/16' piece of poplar wood. Then the 1 3/4' x 2 9/16' poplar wood is attached to the sliding box, 5 1/2' x 5 1/2', with about 6 -- 2 1/2' torque head screws. The 5 1/2' x 5 1/2' box was built with 1 1/8' thick poplar and assembled with the 2 1/2' torque head screws.
Picture with the 4 3/4' tall piece of wood that we used to align the top of the chain with the box. This allowed us to make a slot in the timber that was close to perpendicular with the end of the 6x6 timber. We would slot the 6' x 6' post with the chainsaw and then flip the post over to even out the slot in the post.
We used a 7/16' bell reamer drill bit to clean up the sides and bottom of the 8' deep slot. The 16' long steel knife plate are not perfectly flat-straight. Some of the knife plates have a 1/16' bend in the plate from the laser cut heat. So most of the slots we made were tapered from 1/2' to 7/16' to make the 3/8' steel knife plates fit correctly. We use shims in the slots on some of the knife plates, there weren't a tight fit.
The California Knife Plate Slotter - Mortiser has a depth gauge block in the jig. The knife plates are 16' long with 8' of the knife plate attached to each of the timbers. We set the depth block for an 8 1/4' deep slot. The ends of the steel knife plates should not touch the timber. We used the same depth gauge block for the 5 1/2' x 9' GluLam beams.
The structural plans were drawn with square edged steel knife plates. I got the ok from the structural engineer to chamfer or radius cut the ends of the knife plates, because chainsaws always have a rounded nose. After going thru this process of cutting the slots in timbers for steel knife plates, I think all hidden steel knife plates such be designed with chamfered or radius cut ends.
Okie Knife Plate Slotter - Mortiser for the 5 1/2' x 9' GluLam Beams.
Not a precision slotter, but it's better than free handing the 3/8'x 4'x 8' knife plate slots and it has a depth gauge block so we don't cut the slots too deep. This picture of the Okie Knife Plate Slotter - Mortiser is for the 5' deep slot we had to make in the sides of the 6x6 post and for the 5' deep slots we had to make in the ends of the GluLam beams.
How To Create A Slot In Wood Floors
Erik slides the chainsaw into the router slot and I press down on the Okie knife Plate Slotter jig to keep the chainsaw cut parallel with the sides of the GluLam beams.
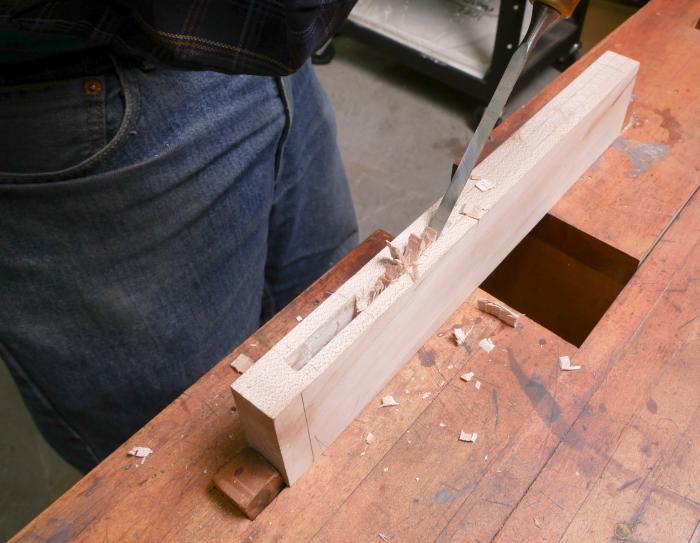
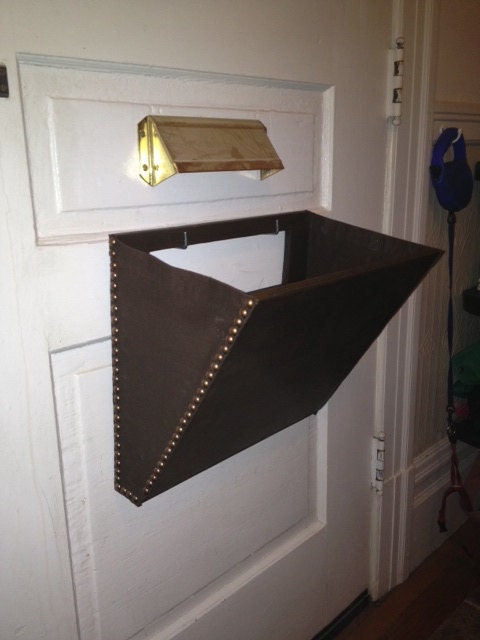
The depth gauge block is also used to keep the jig perpendicular to the cut.To slot the 5 1/2' x 9' Rosboro X-Beam, we used a router jig with a 1/2' straight flute bit. For slots on the ends of the GluLam beams we slotted the beams 4' deep with a 5 1/2' straight flute router bit, an 1' at a time on the depth so we didn't break the router bit. Most of the knife plates are 4' wide. Some were 6' wide on top of the steel columns and 7 1/2' wide on the sides of the columns where the end of the GluLam beams attached. We routed out a 4 1/4' wide slot for the 4' wide knife plates, since the knife plates have a square edge.
:max_bytes(150000):strip_icc()/Dovetailjoints-GettyImages-722324387-5947fa545f9b58d58aa409d9.jpg)
We drilled a couple of holes at each side of the slot with an 7/16' drill bit attached to our ProTool drill guide. To remove the wood the chainsaw didn't-couldn't remove. We would have had the same problem with the Hema or Mafell Chain Slotter with the radius nose on the slotter.
How To Create A Slot In Wooden
Router jig attached to the end of the GluLam beam.
Our newbie painting the ends of the GluLam beams with Anchor Sill to prevent the GluLam beams from checking or splitting in this 100+ degree heat.
Drilling out the steel post base hole an 1/32' . The steel columns must be set perpendicular to the foundation layout to make the knife plates on top of the steel columns align with the knife plate slots in the GluLam beams.
Steel post and steel beams being welded.
How To Make A Keyhole Slot In Wood